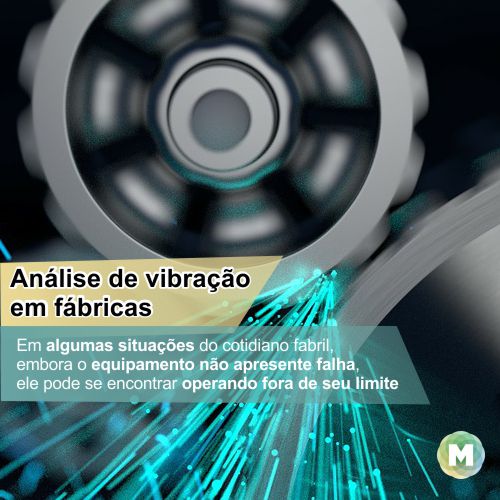
Para se ter uma idéia dos problemas e falhas em potencial que podem ocorrer dentro de um parque fabril, torna-se imprescindível a utilização de Ferramentas de Manutenção Preditiva (Análise de Vibração, Termografia, Análise de Óleo, etc.). Como primeiro passo deve-se estabelecer um roteiro para um mapeamento dos equipamentos e componentes da maior parte do chão de fábrica, visto que nem todos os equipamentos estarão operando no momento das inspeções e alguns, certamente, não permitirão acesso.
Assim como na Medicina são utilizados aparelhos que monitoram a condição física do paciente, também perfaz a mesma condição em relação às Ferramentas de Manutenção Preditiva que vêm a atuar em variáveis, tais como: vibração, temperatura, qualidade do óleo, etc. As variáveis em questão fornecerão subsídios a respeito da saúde do paciente, em outras palavras, da condição dos equipamentos/componentes da Fábrica
Em uma segunda oportunidade ocorre a análise desse material coletado e, nesse estágio, separa-se o “joio do trigo”, ou seja, as condições anormais de funcionamento (falhas em potencial) das condições normais de funcionamento. Após esta separação tenta-se descobrir as causas ou a causa fundamental das anormalidades (ou não conformidades), neste ponto, talvez seja necessário ir até o local para estudar e averigüar o problema mais de perto – “in loco”. Uma vez encontrado o motivo da ocorrência, parte-se para definição “do que fazer” para eliminar o problema e estabelecer o grau de urgência e criticidade para cada caso.
Cabe abordar que nem todas as ocorrências são de fácil e rápida resolução, algumas, possivelmente, necessitarão de medidas paliativas para amenização do problema, visando uma posterior solução.
No ínicio do trabalho, em questão, é costume procurar buscar solução para os casos mais críticos em primeiro lugar (o que poderá levar alguns meses – não há prazo definido), em seguida, os problemas de médio prazo e por último os não críticos. Então, nesta fase, abrem-se as Ordens de Manutenção (OM’s).
Chama-se a atenção neste caso por que, no decorrer do período de Manutenção destas ocorrências, problemas novos irão surgir e, por isso, necessita-se que a velocidade de resolução das ocorrências seja adequada, caso contrário, tem-se excessivas manutenções corretivas, isto é, não se pára de “apagar incêndios”.
A Terceira parte do trabalho refere-se à Manutenção, propriamente dita, neste caso tendo-se definido “o que, quando e como fazer”, parte-se para solução ou amenização da ocorrência. Aqui as Ordens de Manutenção (OM’s) precisam ser cumpridas e, após o cumprimento, deve-se verificar a eficácia da solução (análise crítica) ou da manutenção aplicadas. Certamente, haverá ocorrências que não sendo adequadamente resolvidas necessitarão de nova manutenção, ou seja, haverá retrabalho; ou porque a solução encontrada não foi adequada ou porque a manutenção não obteve a eficácia necessária.
Observação: Em algumas situações do cotidiano fabril, embora o equipamento/componente não apresente falha ou defeito, ele pode se encontrar operando fora de seu limite. Isto pode ocorrer devido à instalação inadequada, dimensionamento e especificação errada ou outra causa externa ao equipamento/componente. Nesta situação, o equipamento/componente irá apresentar desgaste prematuro, por estar operando fora de seus limites.
Mudar este quadro requer investimento e reavaliação da instalação e projetos originais, o que demandará um prazo maior para sua solução. Ás vezes, não se possui este tempo devido ao fato de o equipamento/componente estar já desgastado. Assim, busca-se então um meio de amenizar o problema e conseguir tempo para uma solução mais efetiva do problema. Em manutenção deve-se buscar sempre a solução ideal, não sendo possível esta buscar a melhor solução possível, evitando contudo o abuso ou excesso de “gambiarras” e “gatilhos”.
Fonte: mecatronicaatual.com.br
Foto: Pixabay